Yuzen kimono origins
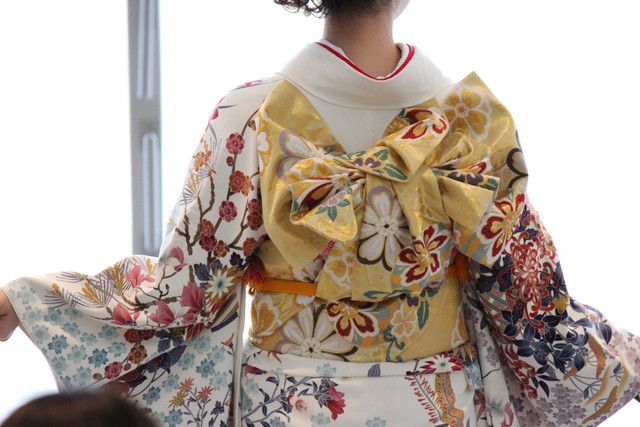
Kaga Yuzen kimono was born when Yuzensai Miyazaki, Printer and dyer, perfected the Edo period, about 300 years ago. The Yuzen process enabled Master Yuzensai and other dyers under the patronage of the fudal of the Kaga district to create beautiful, clear intricate patterns on silk cloth. The Kaga-Zome dyeing method began about 500 years ago using astngency persimmous and the bark of plum trees to create colors ranging from pink to red black. And the basis of today’s Kaga Yuzen kimono was formed when patterns were developed centering around Japanese family crests. Silk-weaving families can be traced to the 15th century in the famous Nishijin weaving center of Kyoto, where elegant fabrics worn by the emperor and the aristocracy were produced. In the 17th century, designs on textiles were applied using stencils and rice paste, in the yuzen or paste-resist method of dyeing. The yuzen method provided an imitation of aristocratic brocades, which were forbidden to commoners by sumptuary laws
Kaga Yuzen kimono pattern
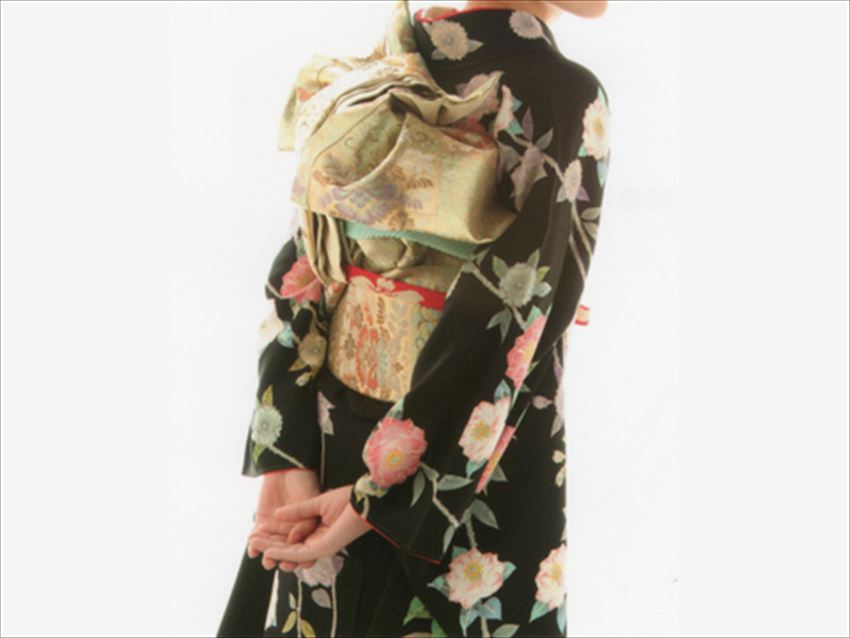
Kaga Yuzen kimono is recognized by the method of shading from the outside to the inside of the patterns and the use of five basic colors, indigo,crimson, chrome yellow, dark green, and royal purple. The designs of Kaga Yuzen kimono depict natural beauty. Flowers, birds, and landscapes are drawn in minute detail with a special paste which prevents the colors from running together. The elaborate designs create handiwork which is gorgeous and graceful. Handmade Kaga-Yuzen is not available in large quantities because of the painstaking planning by each master and the time-consuming work to create a finished piece. Thus, it is not surprising that handmade Kaga-Yuzen is highly appreciated for its artistic value in design and workmanship. Look to Kaga-Yuzen for excellence!
Types of Yuzen kimono
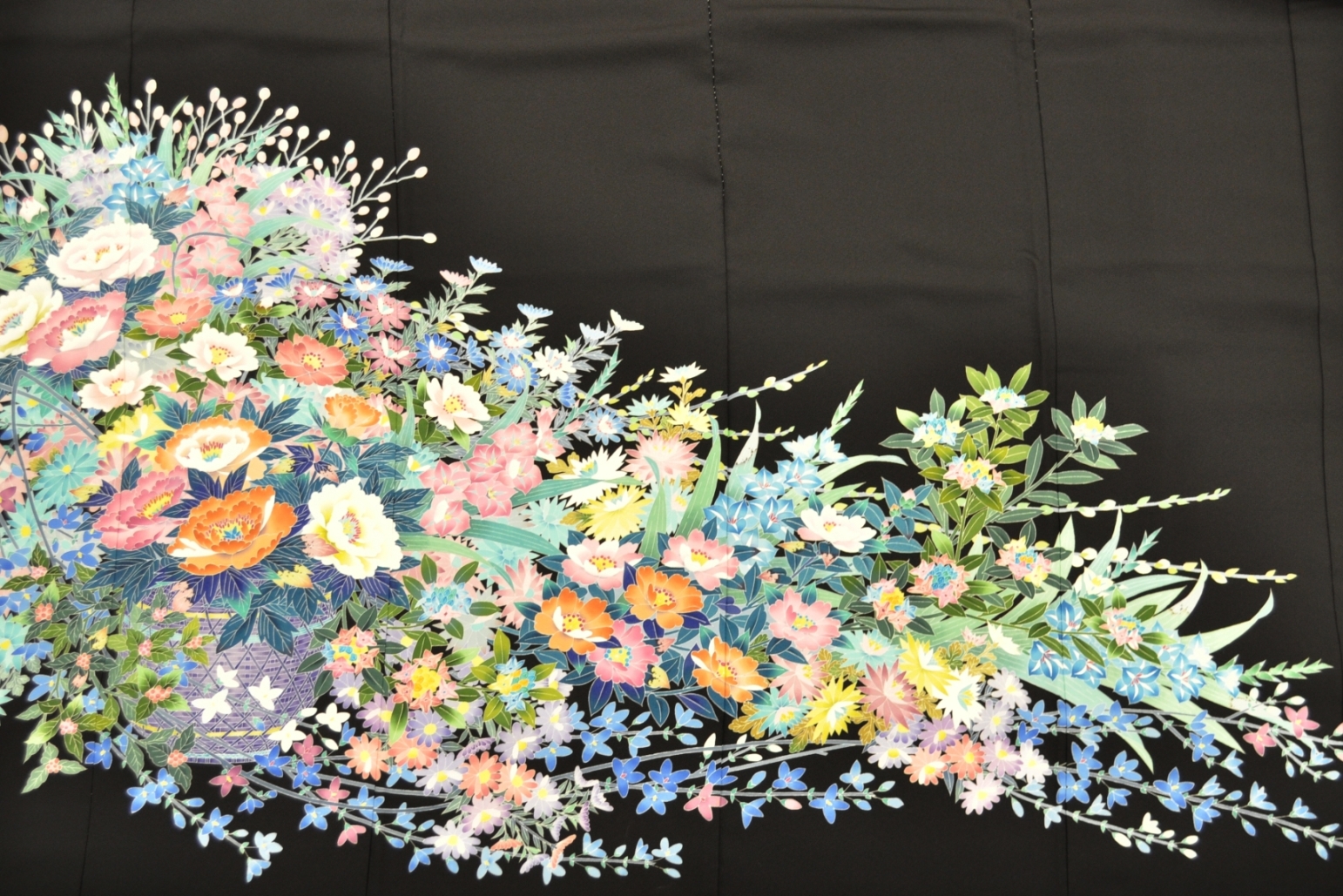
By the late 1980s, an elegant, handwoven, dyed kimono had become extremely costly, running to US$25,000 for a formal garment. In Okinawa the famous yuzen-dyeing method was especially effective where it was produced in the bingata stencil-dyeing techniques, which produced exquisitely colored, striking designs as artistic national treasures. Yuzen has two dyeing styles: “Tegaki Yuzen”, hand painting and “Kata Yuzen, stencil dyeing. “Tegaki Yuzen” is a traditional technique. Its hand-painting skills create quite beautiful and elaborate designs.
Tegaki Yuzen kimono
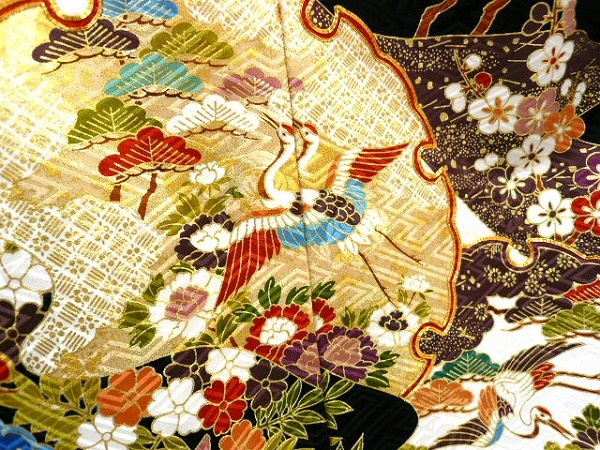
“Tegaki Yuzen” is named differently according to the place in which it was produced: Kyo Yuzen(Kyoto), Kaga Yuzen(Ishikawa) and Tokyo Yuzen(Tokyo). They are the three major Yuzen in Japan. Among these, Kyo Yuzen is considered the most gorgeous and elegant. Kyo Yuzen’s popularity lies in its luxuriouness and fine texture: it is often embroidered with golden yarn and leaf.
Kaga Yuzen kimono
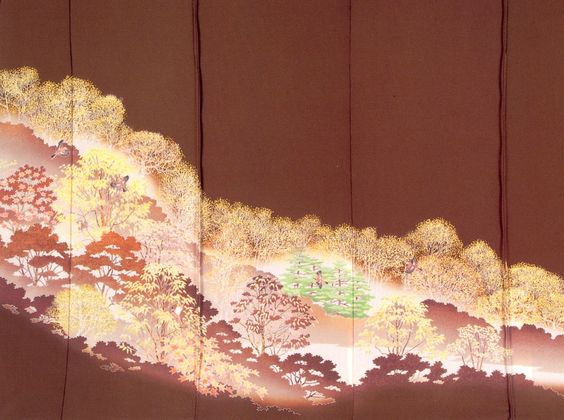
Kaga Yuzen is modest when compared to Kyo Yuzen. It draws on natural objects such as flowers and birds using soft colors. You will be impressed by its elegance and beauty when you see Kaga Yuzen kimono. Tokyo Yuzen is also called Edo Yuzen. It is characterized by its cool and tidy designs. The sense of “wabi and sabi”, Japanese values of culture in the Edo period is reflected in the style.
Kata Yuzen kimono
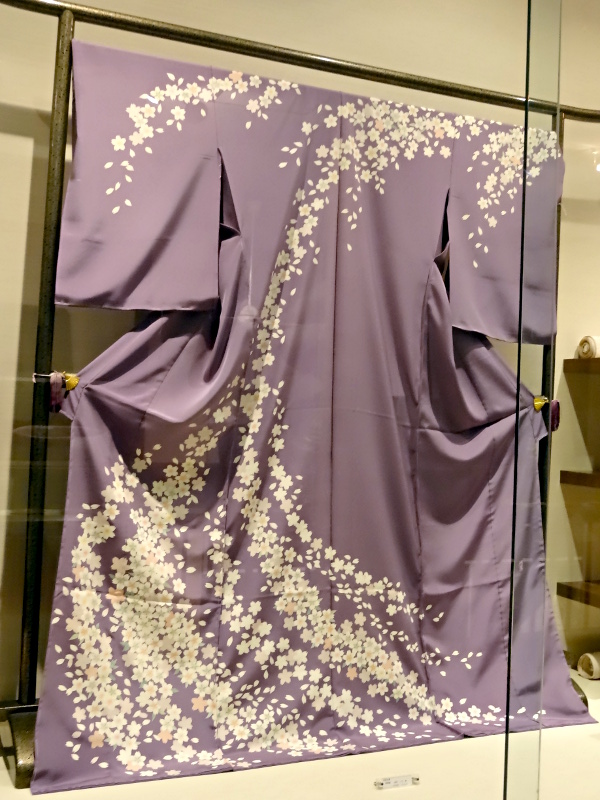
“Kata Yuzen”(stencil dyeing) is a relatively new technique starting from the early Meiji period. The printing technique has made it possible to make Yuzen kimono more quickly and inexpensively than Tegaki Yuzen(hand dyeing). However this technique also requires special skills and its completed designs are no less beautiful than Tegaki Yuzen. Some Yuzen kimono is characterized mainly by this “Yuzen” style. Its popularity lies in its wide variety of traditional and beautiful designs.
The whole process of hand dyeing
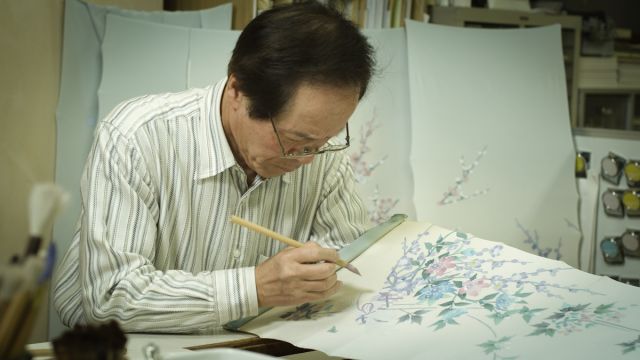
(1) The original design is drawn on the an artist. Designs are usually of natural objects.
(2) White silk cloth is sewn into a kimono.
(3) The drawing on the paper is copied onto the cloth. Both the paper and the cloth are placed on a glass surface withlight coming from below. The ink is washable ; it is made from a herb.
(4) The sewed kimono with drawings is separated into several different parts. The cloth is put on the bamboo support and the artisan traces drawn lines with rice paste from a cone. The lines thus become ‘dye-proof’ or a kind of dike which keeps different colors fromgetting mixed. After the paste is washed away later (process 10) lines remain white. Soybeans are soft in water and smashed. This is thinned with water. The cloth is soaked with this water and dyed over a charcoal fire. This soybean process is done to make the rice paste stay firmly on the cloth.
(5) The comes dyeing. Several kinds of brushes are used. Shading off of colors and worm-eaten leaves in the painting are typical of Kaga-Yuzen, which make the picture look more natural.
(6) The cloth is steamed for 20 minutes to make the colors fast.
(7) The dyed parts of the cloth are coated with rice paste. This will protect these parts in the next process. Soybean water is sprinkled over the cloth to make the next process easier.
(8) Each piece of cloth is sewed onto a long strip. With a brush of deer fur containing ample dye, the artisan brush the whole cloth, dyeing the remaining background. Because of process 7 the parts already dyed remain intact.
(9) The cloth is steamed for 30�\50 minutes with a temperature of 90�\100 degrees centigrade. This will settle the and make them brighter.
(10) The comes the most famous part of people used to see pretty dyed long strips of cloth streaming clear river. This was to wash the paste and unnecessary dyes on the cloth. Now the river are not as clean as they used to be , so in a factory we have a basin with underground water powered electrically. The temperature of this water remains the same (about 14 degrees) all the year round and this is the ideal temperature for cloth washing. Now the anti-pollution movement has made rivers cleaner, so sometimes early in the morning you may be able to see it. Quite a picturesque scene.
(11)The cloth is steamed for adjustment, just like steam-ironing.
(12) If requested , gold and silver embroidery is made and family crests are dyed on the left-over parts. The whole process takes about two or three month. 1 tan is 12 meters long and is for one kimono.